First Mold consolidates 60+ CNC units into a new 0.8km facility near its Gangkou Industrial Park, closing the distant Dongsheng factory to resolve 13.5km production inefficiencies. The move eliminates technician commutes and equipment delays, boosting CNC utilization to 90% while freeing space for new injection machines to increase capacity by 10%. Clients gain faster cycles (e.g., medical modifications reduced 40%) and 5-8% cost savings.
Zhongshan City, Guangdong Province, China, 25th Jul 2025 – First Mold, a precision manufacturing company that has been operating in Zhongshan for fifteen years, is facing a typical dilemma of upgrading a Zhongshan manufacturing company: the old Dongsheng factory, which was opened in 2010, and the First Mold Industrial Park in Gangkou Town, which will go into operation in 2020, are 13.5 kilometers apart, and the decentralized layout is gradually evolving into a shackle of efficiency.
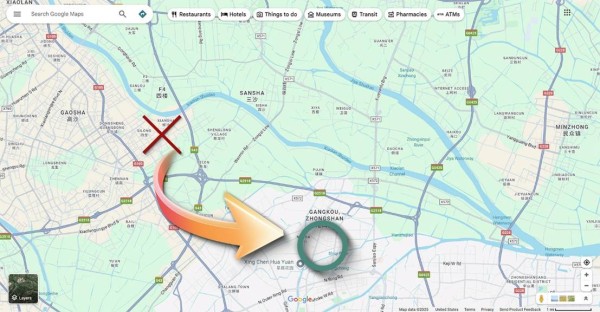
Geographic separation brought about by the company’s progress
General Manager James Li bluntly stated the pain point in an interview:
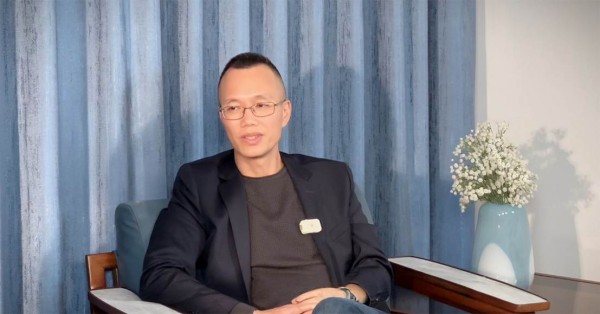
“The CNC machines in both the new industrial park in Gangkou and the old factory are responsible for both rapid prototyping projects and mold making projects. This was a decision made to maximize the efficiency of the machines’ work. Technicians sometimes have to commute over 30 kilometers to coordinate production. This invariably results in a lot of wasted labor hours each year. Sometimes, urgent orders can be delivered up to 6 hours late due to equipment segregation. The establishment of First Mold’s new industrial park was originally a happy event, but unexpectedly it also brought some resistance”
This kind of loss on the client side may indirectly translate into cost pressure.
CNC capacity centralized relocation breakthrough
In the face of continuous accumulation of efficiency loss, First Mold will launch 3 key adjustments in September 2025:
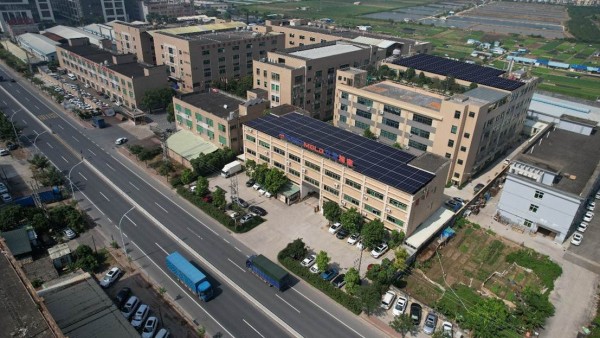
Space consolidation
Lease a new factory building (6,000 square meters) only 0.8 kilometers away from the newly built First Mold Industrial Park, and centralize management of more than 60 sets of CNC equipments dispersed in two places to end the cross-town production mode.
Retirement of the old factory
The Dongsheng base, which has been in service for 15 years, is officially closed, and all the mold manufacturing business it carries is moved to the new CNC center.
Capacity Upgrade
First Mold Industrial Park vacated the space to introduce multiple injection molding machines including JSW, Haitian and other brands, and is expected to increase the monthly production capacity of precision injection molded parts by 10% by the end of the year.
“Relocation is not the purpose, reorganization of manufacturing logic is the essence.” James Li emphasized, “Under the new layout, the technical team commuting to zero, equipment deployment time compression of 80%, the goal is to increase CNC utilization rate to more than 90%.”
The efficiency dividend is transmitted to the global supply chain
For First Mold’s global customers, this capacity consolidation will unleash a triple core benefit: delivery cycle compression, cost elasticity space and service reliability upgrade.
Minami Medical, a medical client, calculates that the cycle time for hearing aid modifications will be shortened from 5 days to 3 days – thanks to the improved response time brought about by the co-location of the technical team.
The increased utilization rate of CNC equipment, coupled with the reduction of logistics costs, has lowered the unit price of processing for small- and medium-volume orders by 5-8%.
Cost control begins with self-innovation
For manufacturers, there may be a point worth pondering: the core of cost reduction and efficiency lies in the benefits to their own management. When the industry is obsessed with chasing the “intelligent” label, First Mold’s decision-making logic is more universal: “We have investigated the introduction of AI scheduling system, but the diagnosis found that: the solution to the loss of the technician’s daily 3 hours of commuting, than any software can be faster to improve the efficiency. ” This reveals the essence of manufacturing cost control: priority optimization of resource allocation rather than blind investment.
Jack Zhang, Secretary General of Zhongshan Mould Industry Association, pointed out:30% of enterprises in China’s Pearl River Delta still have the problem of capacity fragmentation left over from early expansion. Eliminating geographic redundancy and reconfiguring production radius is a more sustainable source of competitiveness than price wars.
About First Mold
Founded in 2010 and headquartered in Zhongshan, China, First Mold specializes in precision mold manufacturing, injection molding, and rapid prototyping. Serving global clients in medical, automotive, and consumer electronics sectors, the company maintains ISO 9001, IATF 16949, and ISO 13485 certified quality systems. With a Mexico production facility, First Mold delivers reliable manufacturing solutions worldwide.
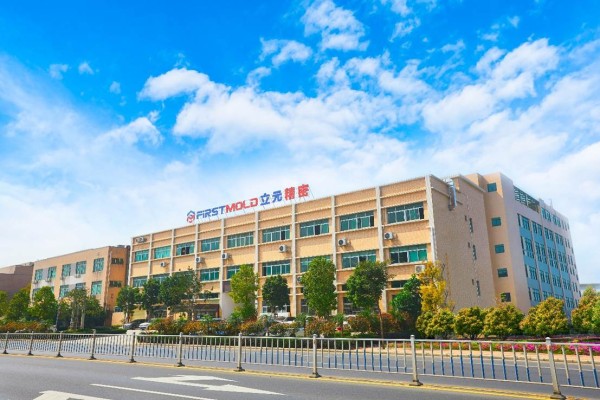
Media Contact
Organization: First Mold Manufacturing Limited
Contact Person: Young Lee
Website: https://firstmold.com/
Email: Send Email
Contact Number: +8618928160183
Address:88 West Shagang Road, Gangkou Town, Zhongshan City, China
City: Zhongshan City
State: Guangdong Province
Country:China
Release id:31428
The post First Mold to relocates CNC capacity centrally to crack efficiency dilemma appeared first on King Newswire. This content is provided by a third-party source.. King Newswire makes no warranties or representations in connection with it. King Newswire is a press release distribution agency and does not endorse or verify the claims made in this release. If you have any complaints or copyright concerns related to this article, please contact the company listed in the ‘Media Contact’ section
Disclaimer: The views, suggestions, and opinions expressed here are the sole responsibility of the experts. No Clear Insight Research journalist was involved in the writing and production of this article.